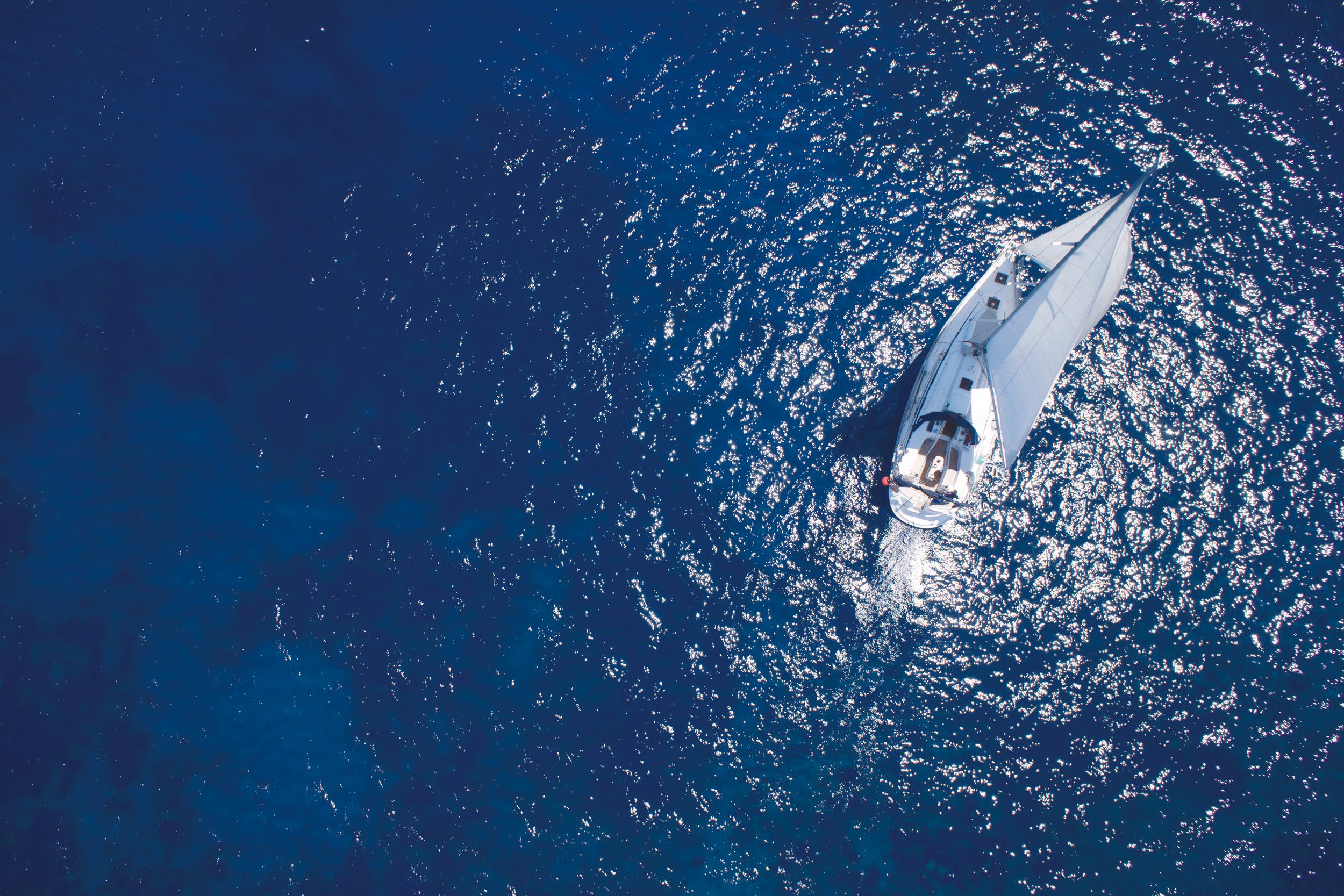
Marblehead
The leading woven cruising sailcloth, available now in Virgin and Recycled Fiber
Technology
Marblehead gets its name from the East-Coast sailing town of Marblehead, Massachusetts. Challenge was asked to develop the highest quality woven for the most demanding and quality conscious sailors. As many sailors know, a boat is fast when its sail keeps its air-foil shape! When a sail stretches and loses its shape, it starts to luff and flutter and does not sail as fast. As a company, Challenge Sailcloth focuses on woven technology. We have not invested in membrane technology, and have continued our pursuit of the best sailcloth. Our philosophy is to make weaves that rely on the strength of their proprietary fibers and constructions.
What matters most for a strong and durable sailcloth is the number of yarn crossings. In a woven fabric yarns pass over the first fiber and curve under the next, ‘locking’ them into each other. It is these yarn crossings, or ‘Interlockings™’, which resist shape distortion. Challenge developed Fiber 104 with the sole intention of creating a fabric with most Fiber Interlockings. When Fiber 104 is woven in both directions of a sailcloth, it leads to a sail that relies on the strength of a tight, dense weave, rather than short-term chemical finishes. It allows sailmakers to design with lighter fabrics in heavier applications. This Interlock technology created Marblehead.
-
As boat design has evolved and rigs have modernized, it has become obvious that a more balanced AP weave would best suit today’s boats and cruising applications, and make for easier decision making for both salesman and designers. Marblehead AP maintains the same technology and philosophy of our proven and trusted Marblehead LA and HA materials.
What matters most for a strong and durable sailcloth is the number of yarn crossings. In a woven fabric yarns pass over the first fiber and curve under the next, ‘locking’ them into each other. It is these yarn crossings, or ‘Interlockings™’, which resist shape distortion. Challenge developed Fiber 104 with the sole intention of creating a fabric with most fiber interlockings.
When Fiber 104 is woven in both directions of a sailcloth, it leads to a sail that relies on the strength of a tight, dense weave, rather than short-term chemical finishes. It allows sailmakers to design with lighter fabrics in heavier applications. This Interlock technology created Marblehead.
-
5.42 Marblehead AP 150 x 350
6.42 Marblehead AP 220 x 420
7.42 Marblehead AP 275 x 570
8.42 Marblehead AP 350 x 700
9.42 Marblehead AP 350 x 1000
10.42 Marblehead AP 440 x 1300
-
Long term performance for cruising sails
Long term UV resistance
Ease of Handling
Low stretch / high modulus due to finishing techniques
Decades of proven performance a life quality on the water
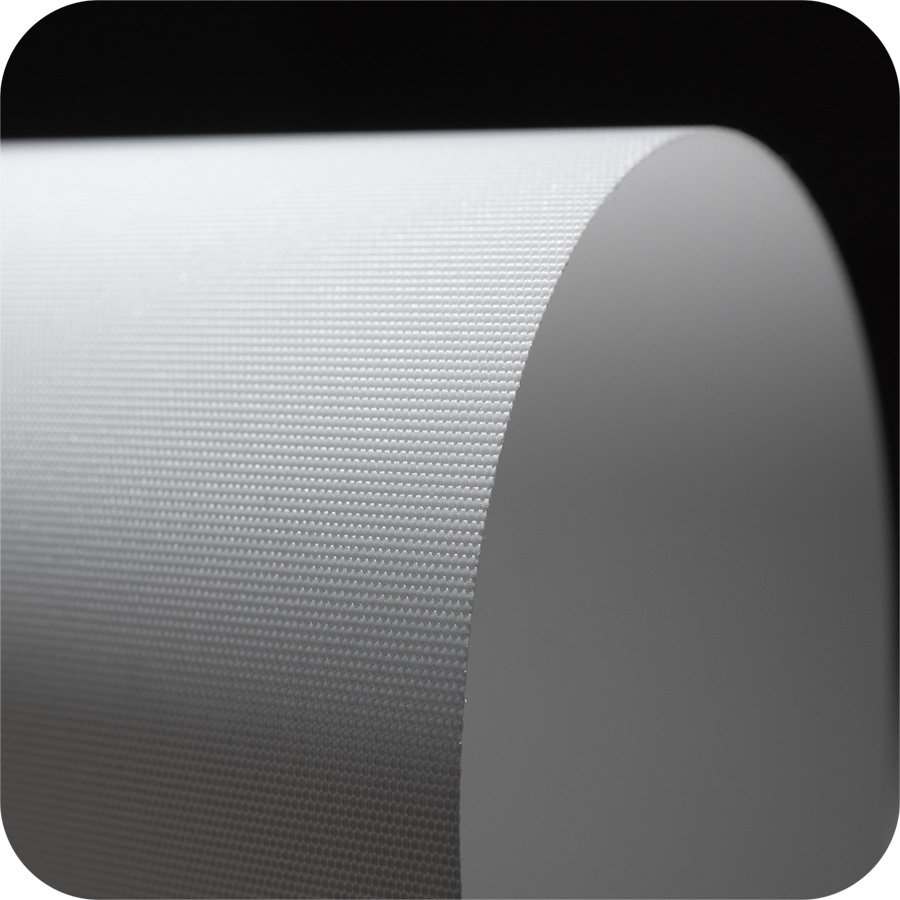
D6.47 Rec
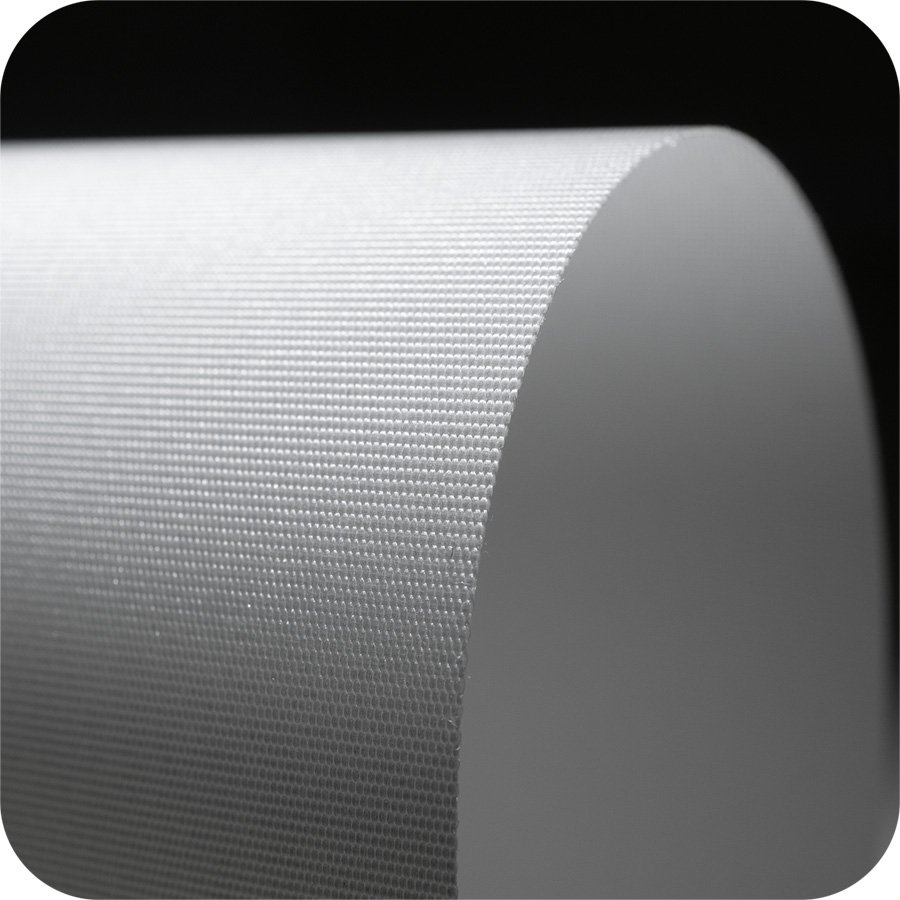
D7.47 Rec
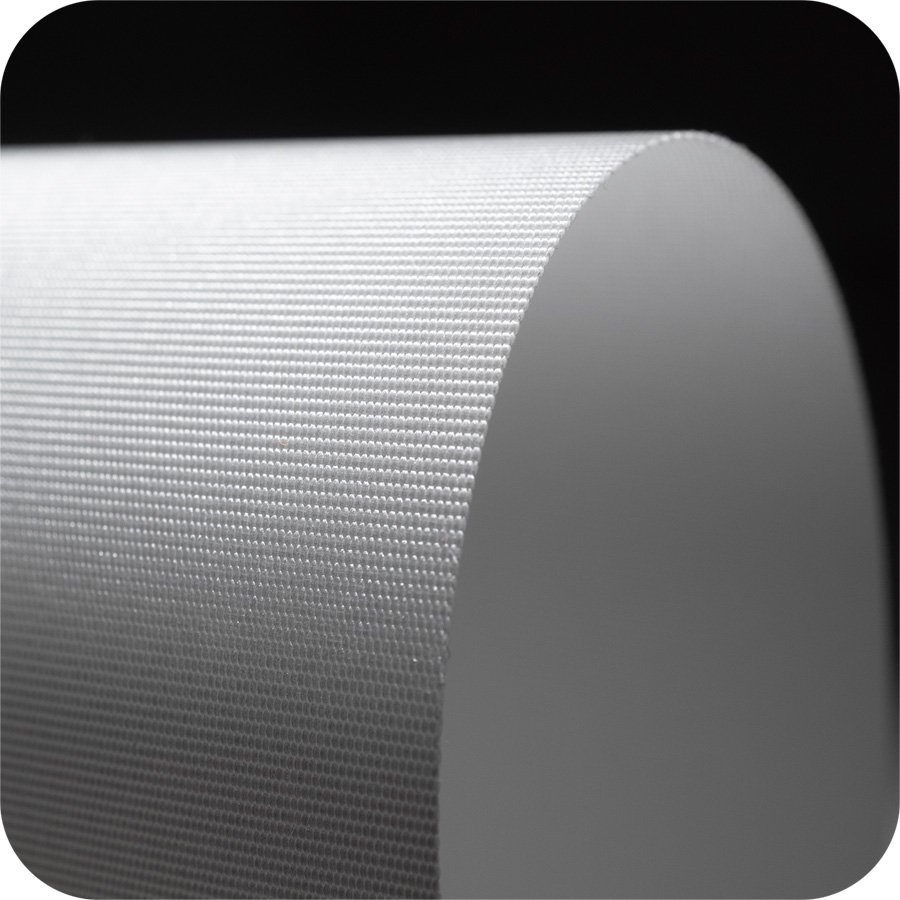
D8.47 Rec
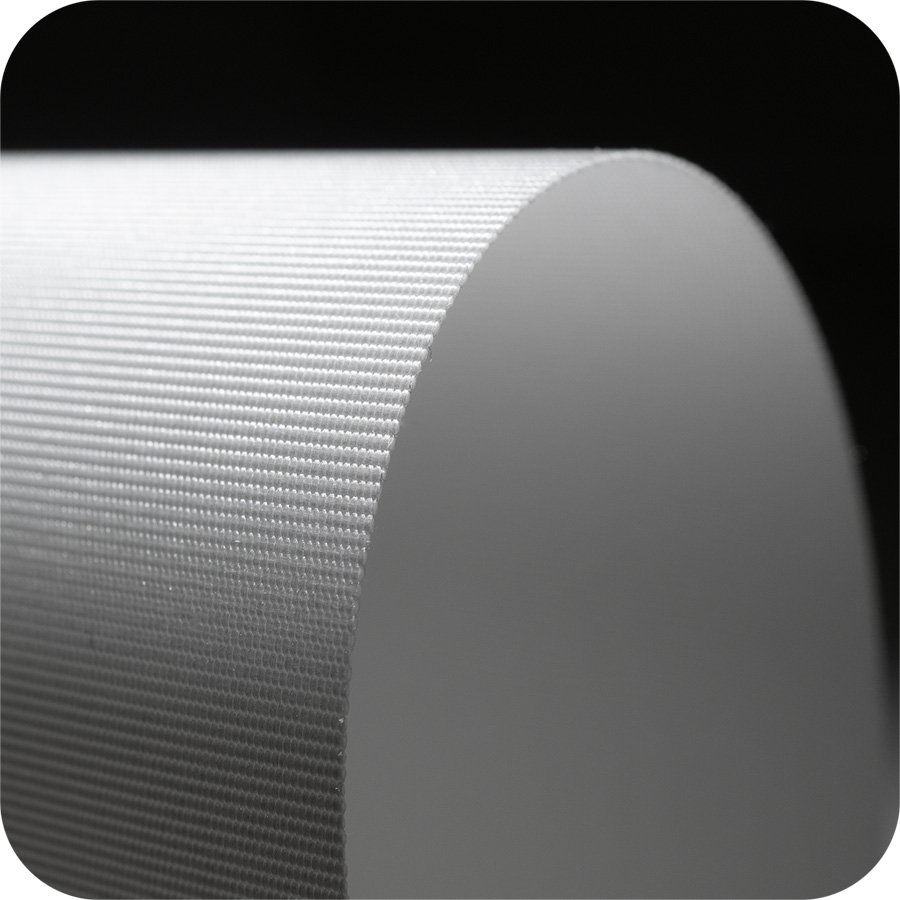
D9.47 Rec
Marblehead
Fabric ID |
Description |
Recycled % of Fiber |
Yarn Denier Warp Fill |
Fabric Width in cm |
D6.47 REC | 6.47 Marblehead REC | 100% | 250 400 | 54 137 |
D7.47 REC | 7.47 Marblehead REC | 100% | 300 500 | 54 137 |
D8.47 REC | 8.47 Marblehead REC | 100% | 300 720 | 54 137 |
D9.47 REC | 9.47 Marblehead REC | 100% | 300 940 | 54 137 |
D10.47 REC | 10.47 Marblehead REC | 100% | 500 1300 | 54 137 |
Marblehead Recycled:
World’s first sailcloth made from fully recycled fiber.
Innovative Development:
Created by Challenge after extensive global material research and testing.
Proprietary Recycled Polyester R104:
Matches the properties of virgin Fiber 104, a first in the industry.
Performance Assurance:
Marblehead REC offers exceptional performance, durability, and UV resistance.
Sustainability Commitment:
Challenge provides these advanced recycled fabrics at the same price as virgin polyester wovens.
Industry Breakthrough:
Represents a significant advancement in woven sailcloth technology.
True Green Solution:
Emphasizes the use of recycled materials over purchasing carbon offsets for sustainability
Marblehead powers the world’s leading yachts
Marblehead was designed and used on the Maltese Falcon by legendary Sailmaker Robbie Doyle. The super tight weaves, long term performance, and durability of the constructions power the yacht. The same fabric used in the maltese falcon is available for yachts ranging from 20-70 feet in single ply, and larger in 2 ply.
Decades of Proven Quality
Thousands of yachts have traveled the world, won coastal sailing races, or enjoyed weekend getaways with Marblehead.
Marblehead Recycled
The superior constructions of Marblehead, now available with recycled fiber. Challenge has taken years of Research and Development and applied Ecopak Technology to Marblehead.
Marblehead Recycled will be available from January 2023.
The Future is Now, and it Can’t Wait.
The legacy of Challenge Sailcloth spans four generations in the sailing textile industry. In 1917, our family founded Howe and Bainbridge, one of the first sailcloth companies in the USA. In the 1930s, DuPont® invented synthetic polyester and nylon fibers which we used to create the first Cordura® nylon mainsail cloth. Moving from tar-impregnated cotton sails to technical synthetic textiles started a new era of sailboat racing and innovation. We’ve been leaders at the forefront of textile innovation for over 100 years. Looking forward, our focus is entirely on sustainability within the textile industry.
In 2020, Challenge Sailcloth launched a new company called Challenge Outdoor, spearheaded by world champion sailor and technical textiles expert, Hale Walcoff. Hale had a vision to produce light, durable, and UV resistant materials for the outdoor sports industry using 100% recycled polyester. He wanted to produce fabrics that were best in class for the industry while being environmentally friendly. Challenge Outdoor is dedicated to reducing real-world carbon emissions and promoting clean textile technology. As outdoor enthusiasts, it is our duty to tackle the climate crisis.
This project would not have been possible as recently as five years ago, because recycled and natural component manufacturers had not achieved the performance levels required in strenuous and demanding outdoor sports. Thankfully, the global community demanded green tech, and the investment followed. Moving full speed ahead, our development efforts will be focused on sustainable innovation across our product lines. This is our new race against the clock and a challenge to the industry. Solving the climate crisis requires world-wide collaboration and we welcome you to get on board.
Sustainability Starts with You
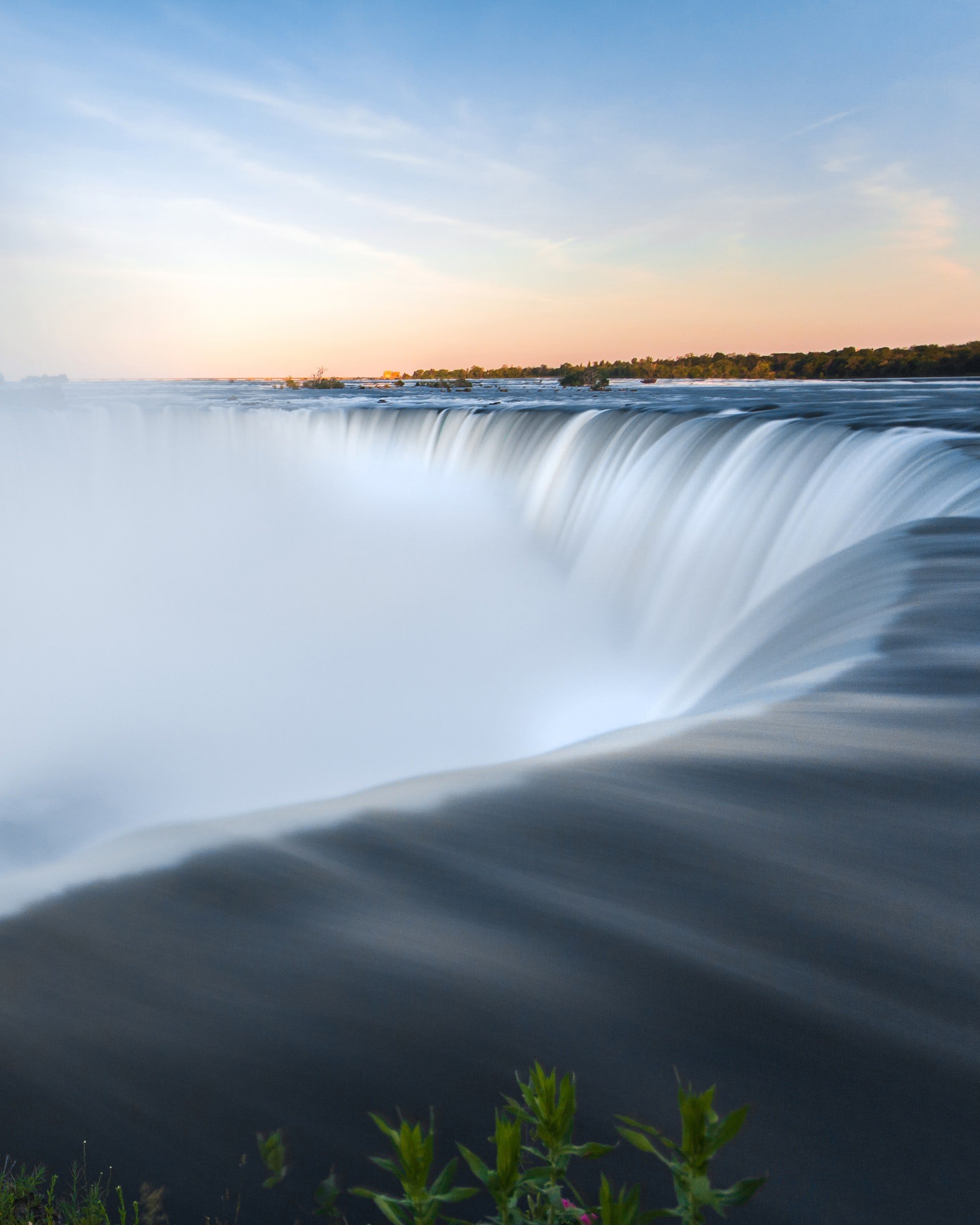
Energy-Efficient Manufacturing
Our textiles are produced at eco-friendly facilities powered by hydroelectric energy.
Our innovative manufacturing system eliminates expensive and energy intensive drying ovens, hot rooms for curing, and many other processes needed to laminate Nylon and Polyester with solvent-based adhesive.
We maintain stock in both the U.S. and Asia for better efficiency with our manufacturing partners and brands.