Technology
Warp-Drive styles are the best choice for sailors who desire the performance of a laminate, but want the durability of a woven. Warp-Drive styles have much lower stretch in the warp direction and therefore in a radial configuration have better shape holding ability than traditional crosscut Dacron sails. But unlike laminates, they will not mildew, delaminate or crack over time.
Warp-Drive styles are all made with very low crimp for ultimate performance.
The prefect balance between Price, Performance, and Durability.
The only true warp Dacron material on the market today.
Excellent option for both performance cruisers and Club Racers.
Attractive price point.
Warp Drive
Fabric ID |
Description |
Warp DPI |
Fabric Width in cm |
D4.11WD | 4.11 Warp-Drive Race | 19,000 | 54 137 |
D6.11WD | 6.11 Warp-Drive Race | 27,000 | 54 137 |
D7.41WD | 7.41 Warp-Drive Race | 27,000 | 54 137 |
D8.71WD | 8.71 Warp-Drive Race | 33,600 | 54 137 |
The Future is Now, and it Can’t Wait.
The legacy of Challenge Sailcloth spans four generations in the sailing textile industry. In 1917, our family founded Howe and Bainbridge, one of the first sailcloth companies in the USA. In the 1930s, DuPont® invented synthetic polyester and nylon fibers which we used to create the first Cordura® nylon mainsail cloth. Moving from tar-impregnated cotton sails to technical synthetic textiles started a new era of sailboat racing and innovation. We’ve been leaders at the forefront of textile innovation for over 100 years. Looking forward, our focus is entirely on sustainability within the textile industry.
In 2020, Challenge Sailcloth launched a new company called Challenge Outdoor, spearheaded by world champion sailor and technical textiles expert, Hale Walcoff. Hale had a vision to produce light, durable, and UV resistant materials for the outdoor sports industry using 100% recycled polyester. He wanted to produce fabrics that were best in class for the industry while being environmentally friendly. Challenge Outdoor is dedicated to reducing real-world carbon emissions and promoting clean textile technology. As outdoor enthusiasts, it is our duty to tackle the climate crisis.
This project would not have been possible as recently as five years ago, because recycled and natural component manufacturers had not achieved the performance levels required in strenuous and demanding outdoor sports. Thankfully, the global community demanded green tech, and the investment followed. Moving full speed ahead, our development efforts will be focused on sustainable innovation across our product lines. This is our new race against the clock and a challenge to the industry. Solving the climate crisis requires world-wide collaboration and we welcome you to get on board.
Sustainability Starts with You
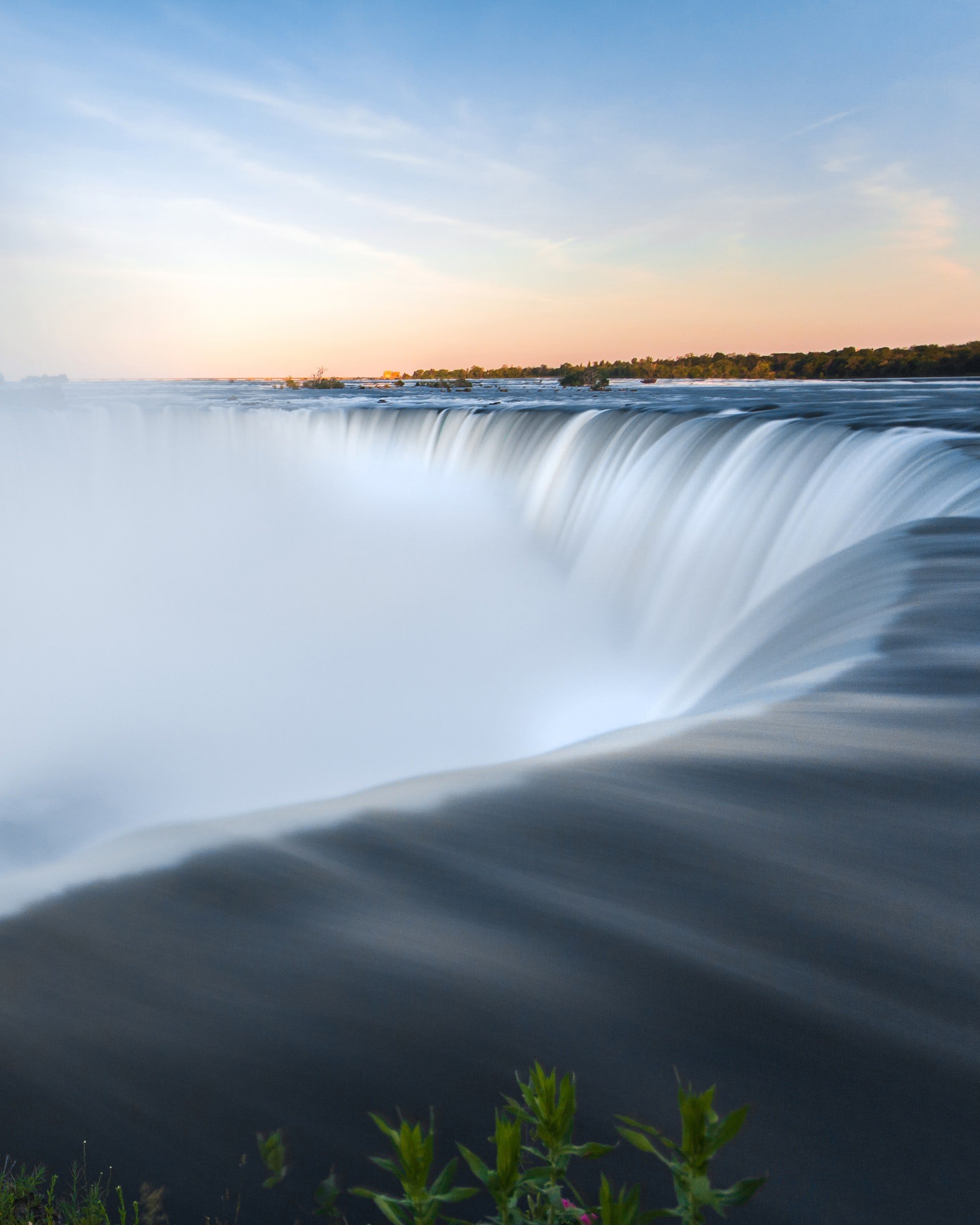
Energy-Efficient Manufacturing
Our textiles are produced at eco-friendly facilities powered by hydroelectric energy.
Our innovative manufacturing system eliminates expensive and energy intensive drying ovens, hot rooms for curing, and many other processes needed to laminate Nylon and Polyester with solvent-based adhesive.
We maintain stock in both the U.S. and Asia for better efficiency with our manufacturing partners and brands.