
OD-TEC
Technology
Challenge is excited to announce OD-Tec, our nascent line of new One Design fabrics designed to challenge the long term status quo in dingy racing sailcloth. Specifically conceived as the next generation of OD materials with a woven structure designed with our superior coating technology in mind. Challenge has developed this unique new range of fabrics to meet not only performance requirements for high level racing, but also to vastly improve durability of the sails. OD-Tec uses high tenacity fibers and proprietary immersion coating chemistry to make a high performance but durable OD sail fabric which has low stretch, superior tear strength and the ability to withstand flogging and abuse on the start line without having the coating white out after a couple of regattas.
-
• OD-TEC fabrics are firm bias, low crimp, and low stretch.
• Prominent Double-Beam matrix ripstop pattern for rugged durability.
• New immersion-coating technology.
• Proprietary chemistry for high performance and superior durability.
• No coating white-out, excellent adhesion. Probably the best coating durability available.
• OD-Tec has tear and breaking strength not seen to date in light weight Dacron fabrics.
• High tenacity fibers and a woven construction developed for Kitesurf and Wing-Foiling fabric technology.
-
2.5 Medium Firm: 3.11 oz Very light weight crosscut or radial.
2.85 Firm: 3.40 oz Crosscut or Radial. A balanced fabric with a slight crosscut tilt. Very high strength to weight ratio.
3.75 Firm: 4.07 oz More crosscut oriented than lighter weights.
-
OD-Tec is designed to Win Races. Nothing else.
OD-Tec
Fabric ID |
Description |
Bias |
Weight SM oz gsm |
Width in cm |
OD-Tec 2.5 | Very light weight crosscut or radial fabric | Medium | 3.11 133 | 60 150 |
OD-Tec 2.85 | Balanced w/crosscut tilt; High strength/wt. ratio | Firm | 3.40 146 | 60 150 |
OD-Tec 2.85 REC | Made with 100% Recycled Fibers | Firm | 3.40 146 | 60 150 |
OD-Tec 3.75 | More crosscut oriented than lighter weights | Firm | 4.07 174 | 60 150 |
Modern One Design Race
Alejandro Pareja González wins a regatta on the first Trial with OD-TEC
Alejandro Pareja González
Wind conditions were light 5-8kt on the first and second day but medium 8-15kt on the last day of racing, perfect conditions for my all round design
GOOD POINTS
Construction
Roll width: 153cm is good as i can cut the whole sail in two frames in my plotter/cutter reducing working time
Soft cutting: plotter/cutter works smoothly into this softer cloth
Easy sewing: thread is crossing easily through the fabric and the machine work it smoothly
Sailing
Increased wind range: soft cloth finish allows better sail shape control of the profile entry working with cunningham trim to balance the F/A mast bend without extra twisting sideways and then getting better pointing ability with power to perform in choppy conditions. On the last race 12-15kt i was full power flying upwind and it was key to wind gold
Downwind: soft cloth finish allows flexibility for continuous mainsheet trim going with twisted leech in light/medium winds
Fill strength: it was enough for light and medium winds but we don't know what will happen in stronger breeze...
Look
Quality: aspect is shinny white which is looking better than the other dacrons which use to look a bit yellow
Degradation
I still don't have any crack on the front of the batten pockets which use to be a critical area. More sailing hours needed to check this but it's looking good!
The Future is Now, and it Can’t Wait.
The legacy of Challenge Sailcloth spans four generations in the sailing textile industry. In 1917, our family founded Howe and Bainbridge, one of the first sailcloth companies in the USA. In the 1930s, DuPont® invented synthetic polyester and nylon fibers which we used to create the first Cordura® nylon mainsail cloth. Moving from tar-impregnated cotton sails to technical synthetic textiles started a new era of sailboat racing and innovation. We’ve been leaders at the forefront of textile innovation for over 100 years. Looking forward, our focus is entirely on sustainability within the textile industry.
In 2020, Challenge Sailcloth launched a new company called Challenge Outdoor, spearheaded by world champion sailor and technical textiles expert, Hale Walcoff. Hale had a vision to produce light, durable, and UV resistant materials for the outdoor sports industry using 100% recycled polyester. He wanted to produce fabrics that were best in class for the industry while being environmentally friendly. Challenge Outdoor is dedicated to reducing real-world carbon emissions and promoting clean textile technology. As outdoor enthusiasts, it is our duty to tackle the climate crisis.
This project would not have been possible as recently as five years ago, because recycled and natural component manufacturers had not achieved the performance levels required in strenuous and demanding outdoor sports. Thankfully, the global community demanded green tech, and the investment followed. Moving full speed ahead, our development efforts will be focused on sustainable innovation across our product lines. This is our new race against the clock and a challenge to the industry. Solving the climate crisis requires world-wide collaboration and we welcome you to get on board.
Sustainability Starts with You
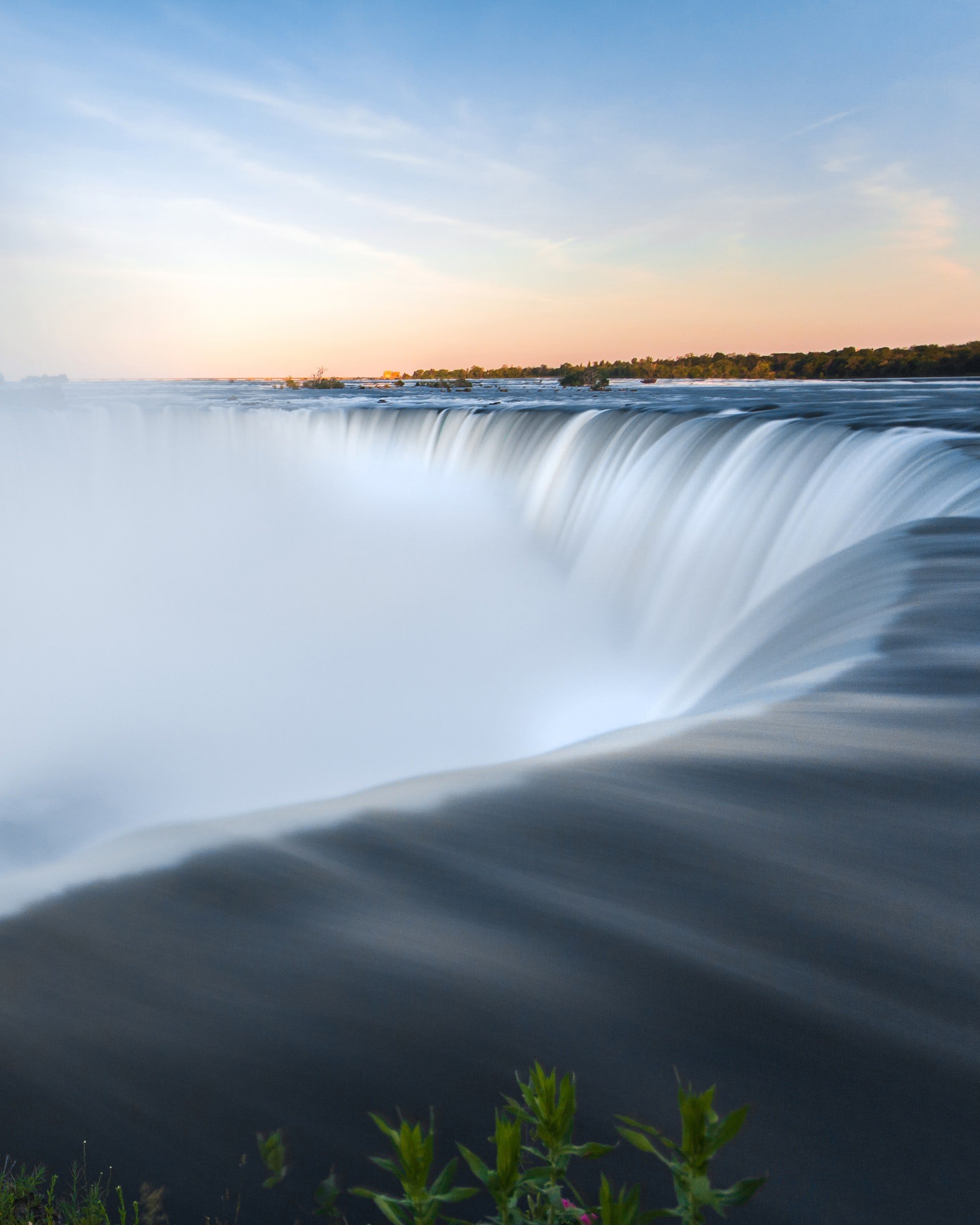
Energy-Efficient Manufacturing
Our textiles are produced at eco-friendly facilities powered by hydroelectric energy.
Our innovative manufacturing system eliminates expensive and energy intensive drying ovens, hot rooms for curing, and many other processes needed to laminate Nylon and Polyester with solvent-based adhesive.
We maintain stock in both the U.S. and Asia for better efficiency with our manufacturing partners and brands.