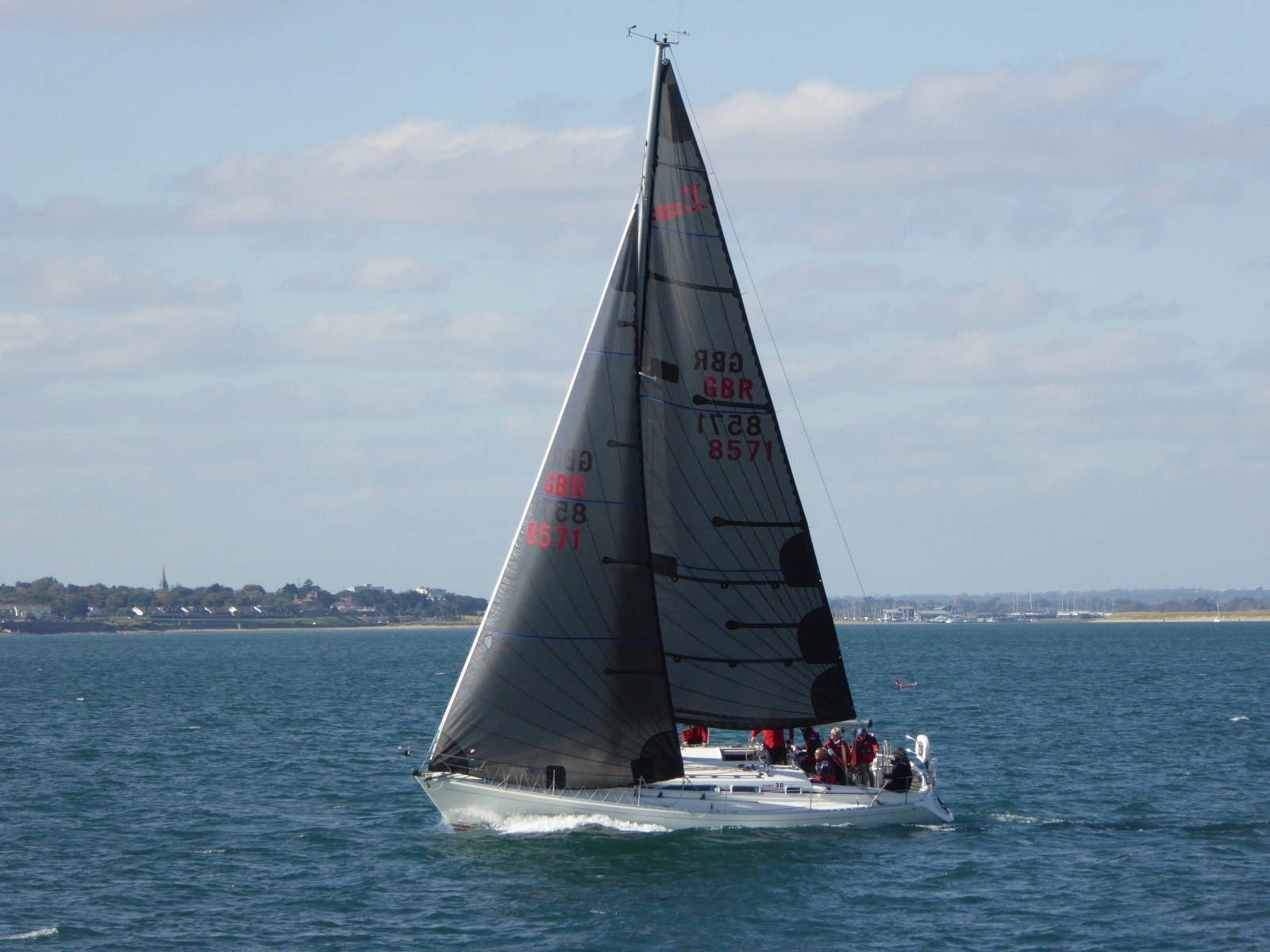
XRP SPORT
Technology
These durable and high value sailcloth polyester styles are a great choice for classes that restrict the use of exotic fibers. XRP styles were designed with high strength to weight ratios. They use efficient fiber inlays without square scrims for reduced weight and increased off angle load bearing capacity. XRP uses high tenacity black coated fibers that have good UV and tear resistance. Constructions are black high tenacity polyester warp, substantial bias X inserts, precision laminated. XRP fabrics are perfect for racing and club racing headsails and mainsails, multihull screechers, various reinforcements, and large yacht code zeros.
This year we introduce our new high modulus line of XRP for bigger boats and higher load cases requiring more sail shape holding ability for your more performance orientated sailors. This line employs 100% high performance warp fibers, both aramid and UPE, for superior stretch resistance which translates to boat speed as the wind and loads increase. The UPE component adds toughness and extra breaking strength over the long haul. All fibers are black across both the polyester and Ultra Aramid lines, hence different materials can be used on the same boat for different sails, or for stepped constructions within individual sails.
-
High Tenacity 100% Recycled Black Polyester Warp Inserts
High Tenacity 100% Recycled Black Polyester X Inserts
Challenge RUV (Recyceld UV Film)
Enhanced for UV and Mildew Protection
-
Used on Upwind Mainsails, Jibs, Racing Genoas - All Polyester for PHRF ratings
Used on larger boat code zeros
High Strength to weight ratios
-
XRP sport enables sailmakers to build performance race sails with all polyester constructions.
The efficient fiber laydowns allow high performance without the use of exotic fibers such as Aramids and Carbon
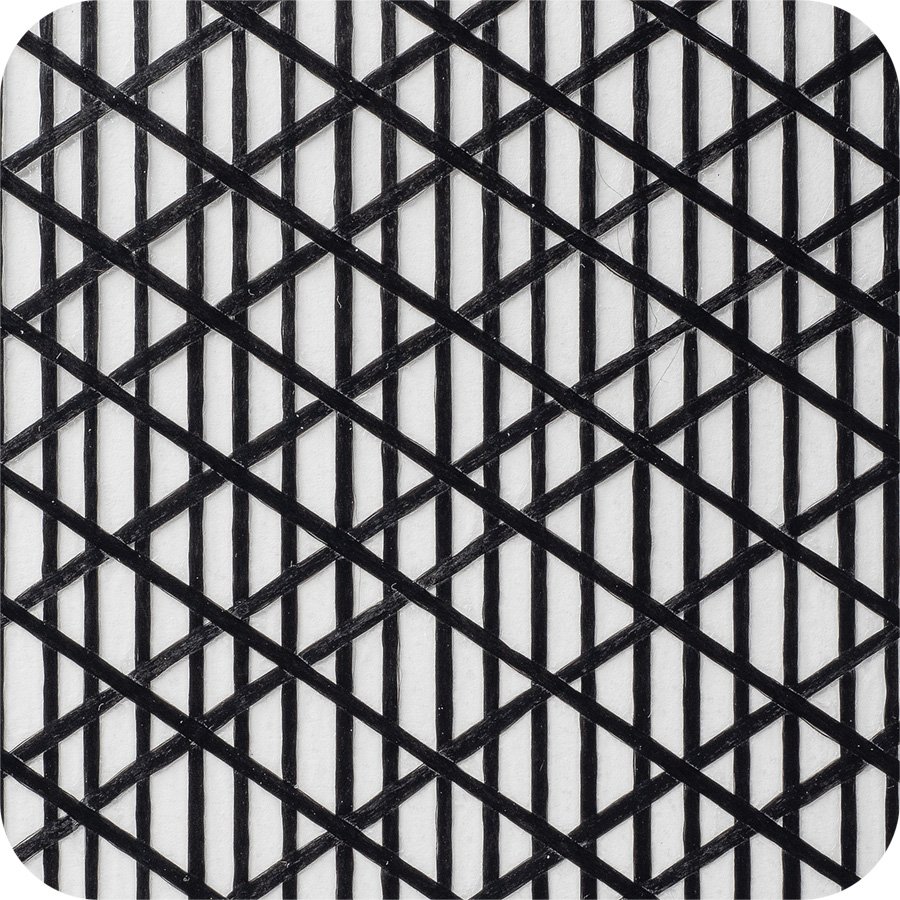
XRP6
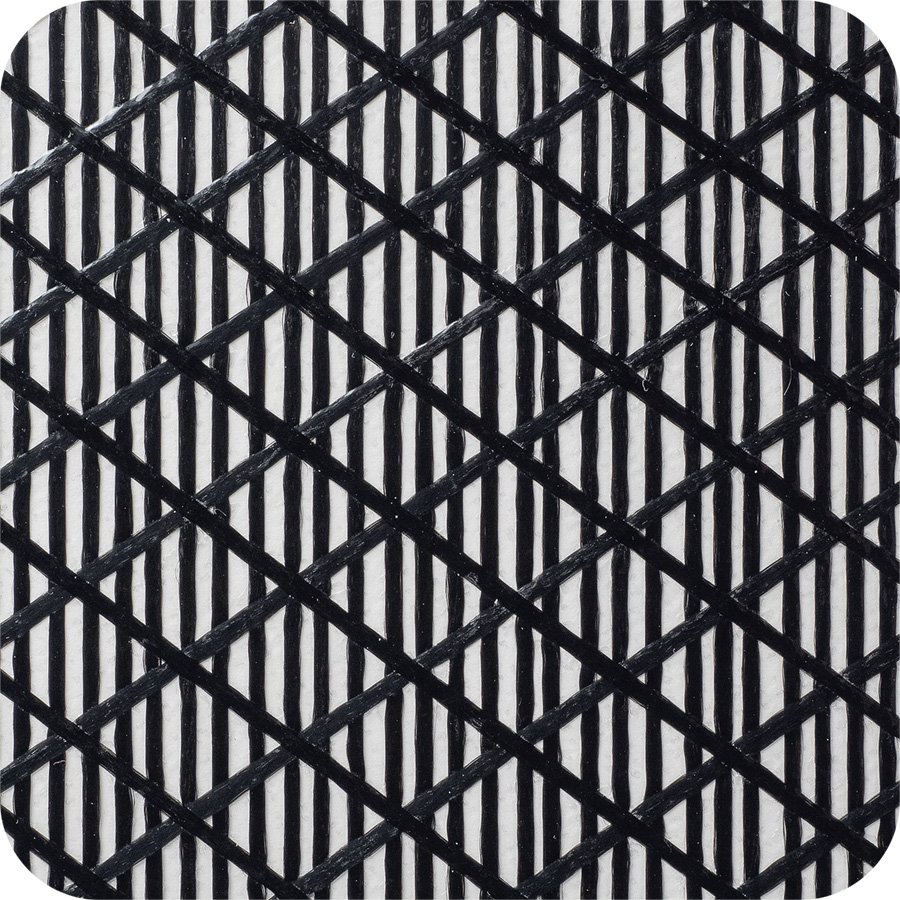
XRP9
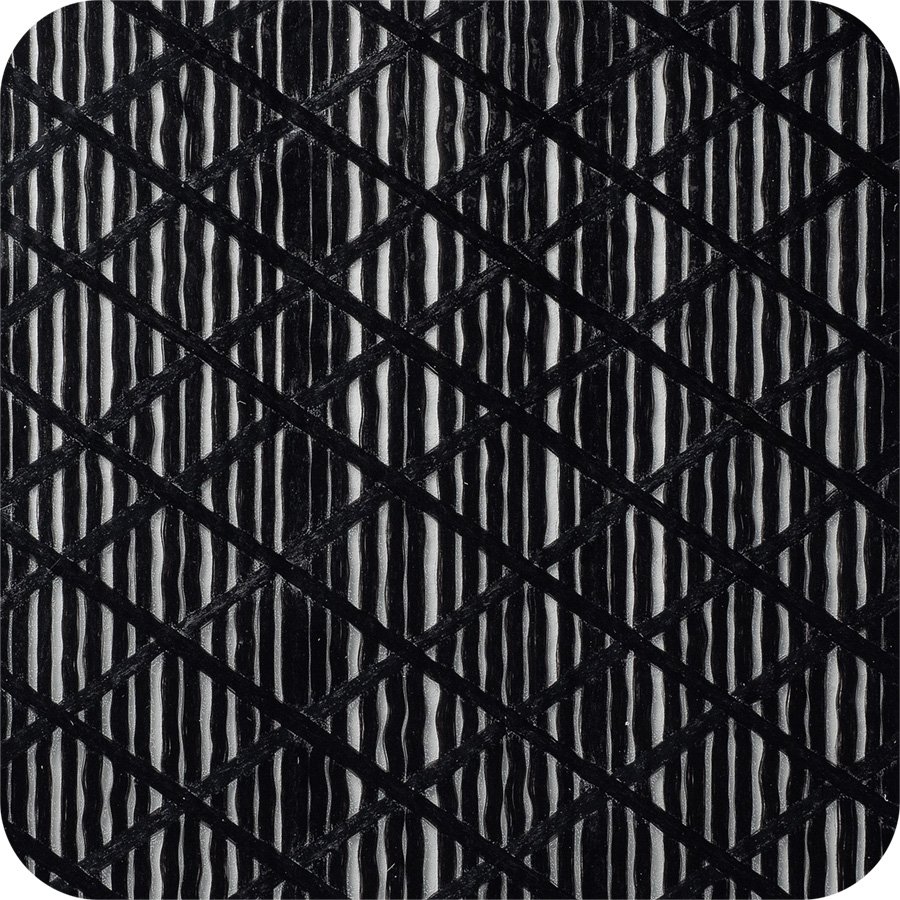
XRP13
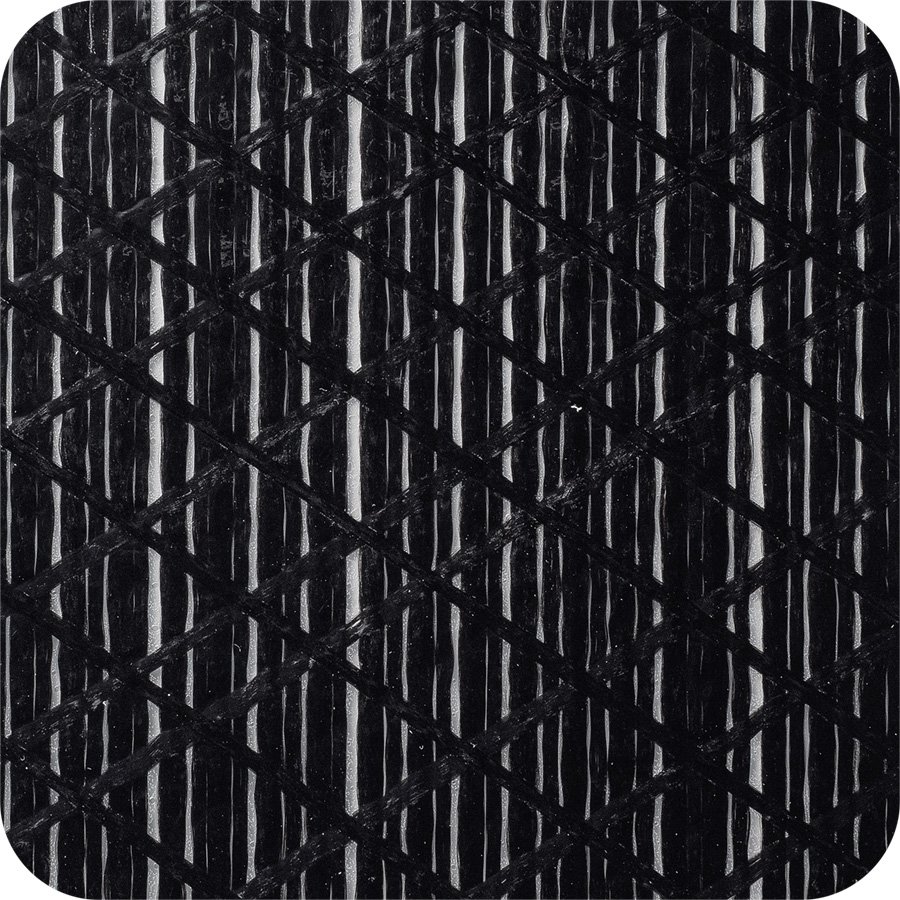
XRP18
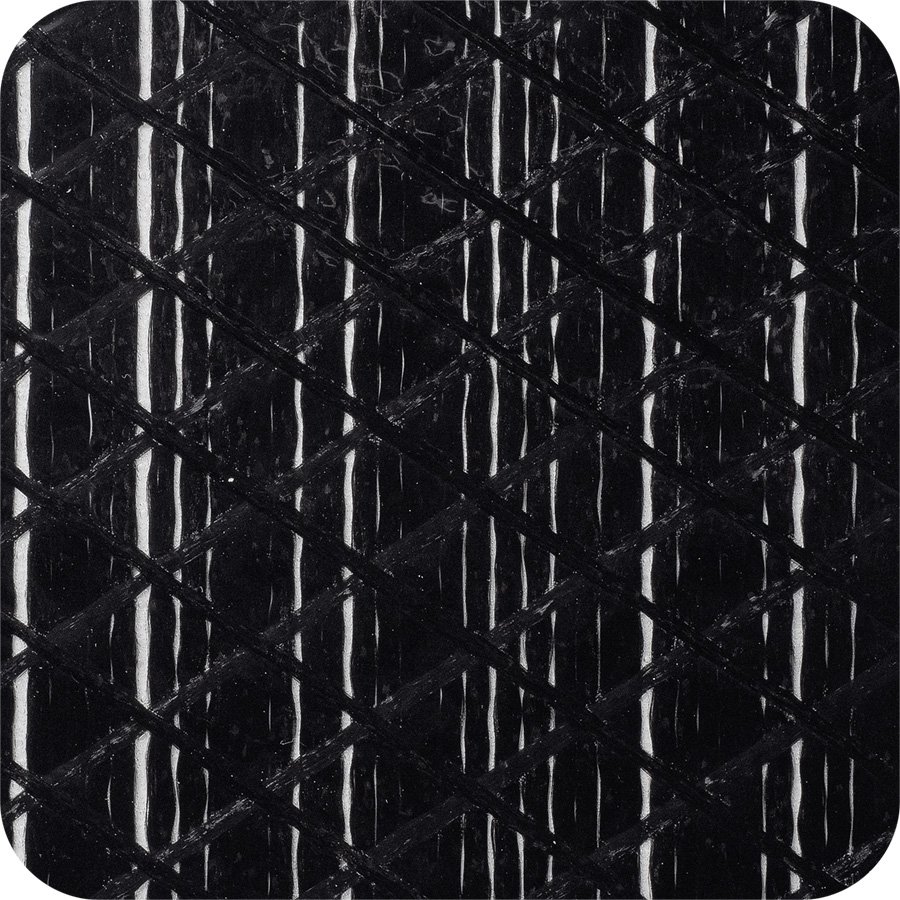
XRP24
XRP
Fabric ID |
Insert DPI Total X 45°/1.5" |
Film |
Weight SM oz gsm |
Width in cm |
XRP6 | 6,000 3,000 | 1.50 | 3.04 130 | 60 150 |
XRP9 | 9,000 3,000 | 1.50 | 3.74 160 | 60 150 |
XRP13 | 12,000 3,000 | 1.50 | 4.44 190 | 60 150 |
XRP18 | 18,000 3,000 | 1.50 | 5.14 220 | 60 150 |
XRP24 | 24,000 3,000 | 2.00 | 6.14 263 | 60 150 |
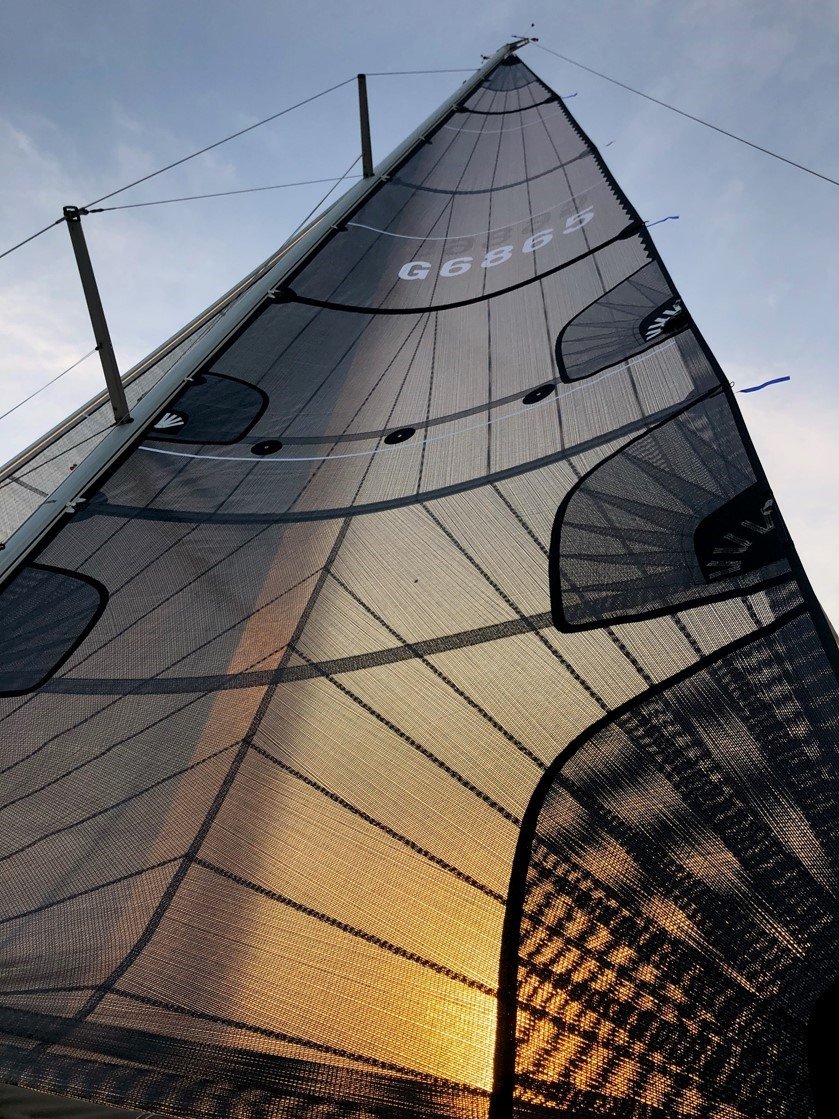
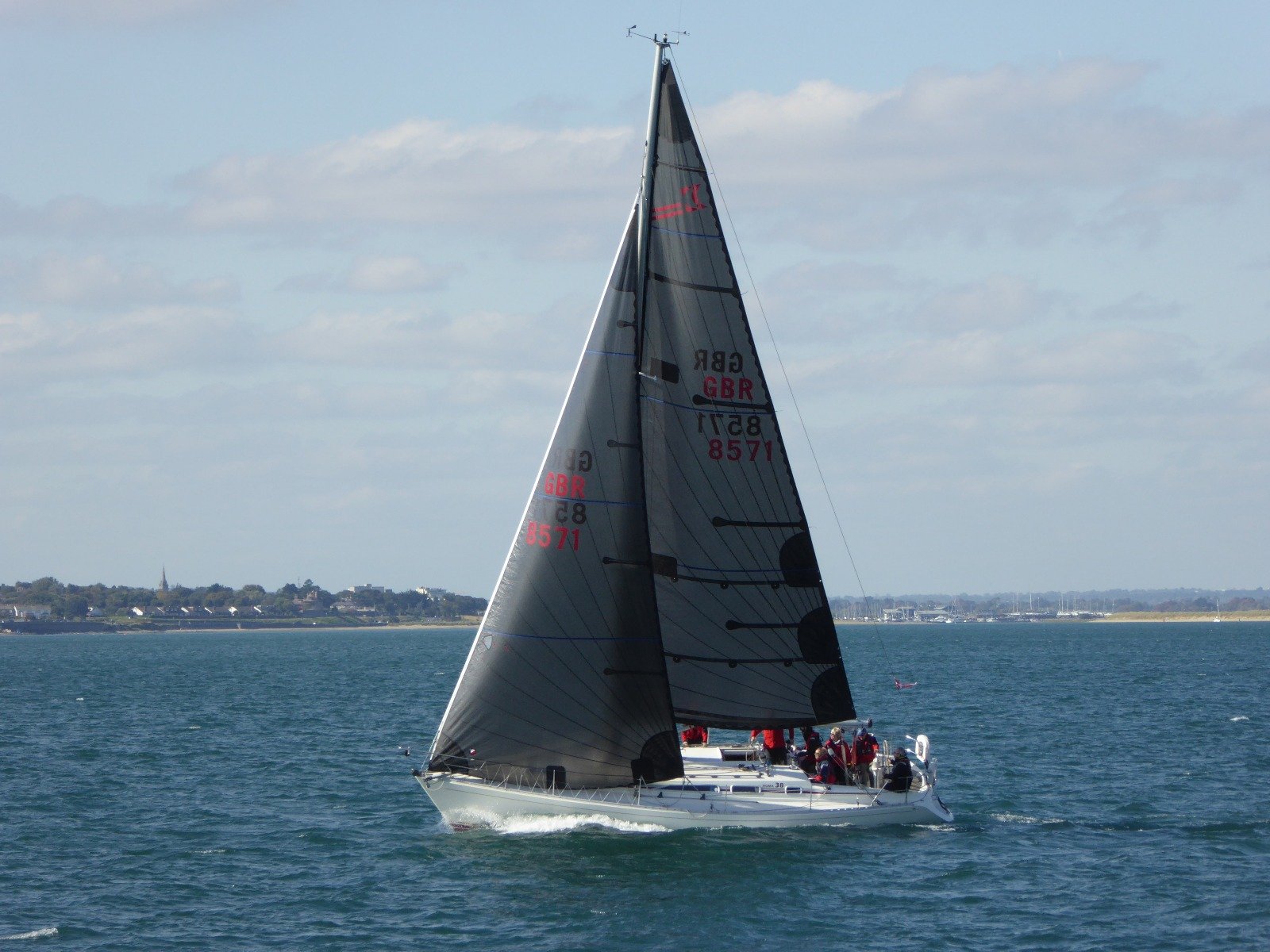
The Future is Now, and it Can’t Wait.
The legacy of Challenge Sailcloth spans four generations in the sailing textile industry. In 1917, our family founded Howe and Bainbridge, one of the first sailcloth companies in the USA. In the 1930s, DuPont® invented synthetic polyester and nylon fibers which we used to create the first Cordura® nylon mainsail cloth. Moving from tar-impregnated cotton sails to technical synthetic textiles started a new era of sailboat racing and innovation. We’ve been leaders at the forefront of textile innovation for over 100 years. Looking forward, our focus is entirely on sustainability within the textile industry.
In 2020, Challenge Sailcloth launched a new company called Challenge Outdoor, spearheaded by world champion sailor and technical textiles expert, Hale Walcoff. Hale had a vision to produce light, durable, and UV resistant materials for the outdoor sports industry using 100% recycled polyester. He wanted to produce fabrics that were best in class for the industry while being environmentally friendly. Challenge Outdoor is dedicated to reducing real-world carbon emissions and promoting clean textile technology. As outdoor enthusiasts, it is our duty to tackle the climate crisis.
This project would not have been possible as recently as five years ago, because recycled and natural component manufacturers had not achieved the performance levels required in strenuous and demanding outdoor sports. Thankfully, the global community demanded green tech, and the investment followed. Moving full speed ahead, our development efforts will be focused on sustainable innovation across our product lines. This is our new race against the clock and a challenge to the industry. Solving the climate crisis requires world-wide collaboration and we welcome you to get on board.
Sustainability Starts with You
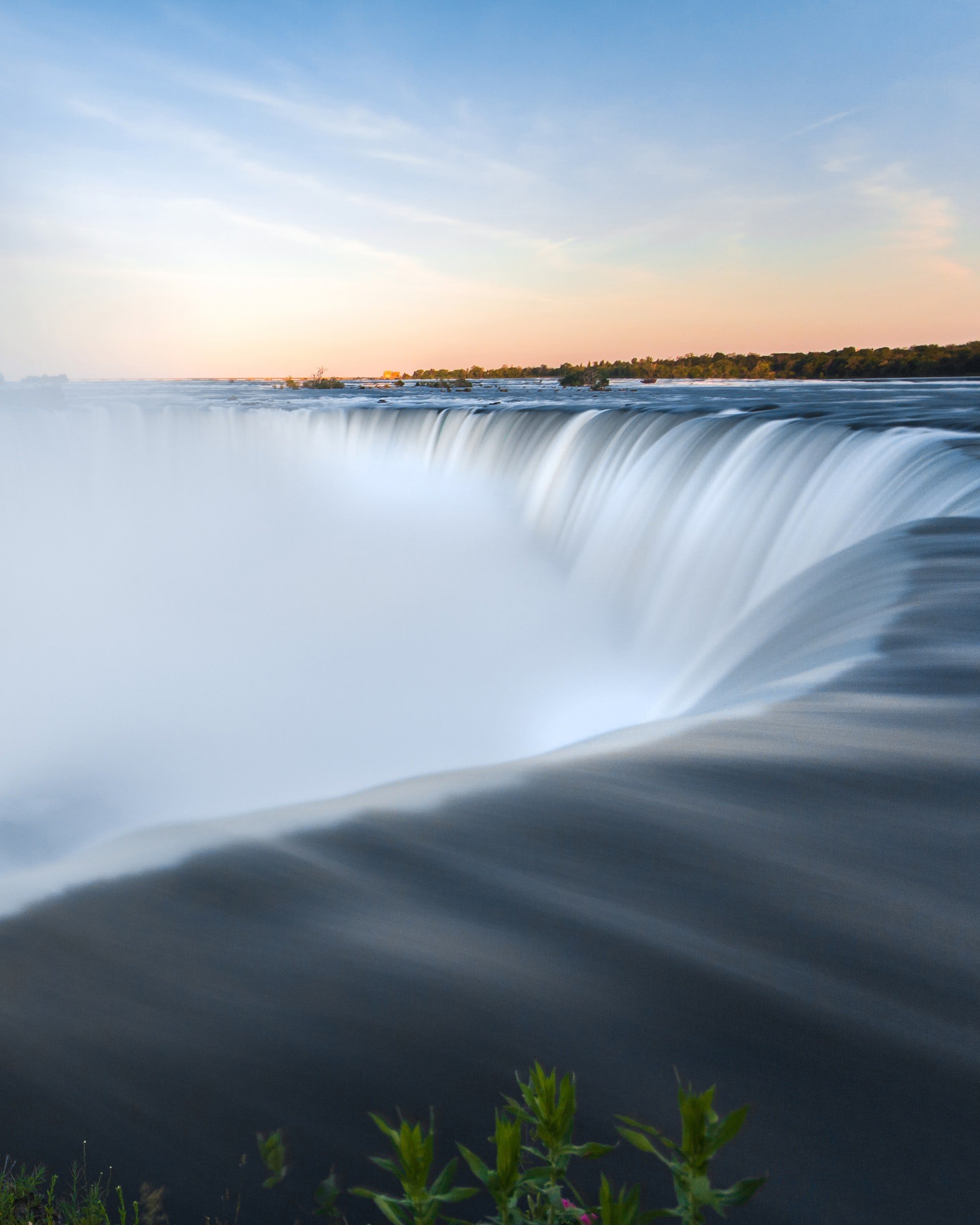
Energy-Efficient Manufacturing
Our textiles are produced at eco-friendly facilities powered by hydroelectric energy.
Our innovative manufacturing system eliminates expensive and energy intensive drying ovens, hot rooms for curing, and many other processes needed to laminate Nylon and Polyester with solvent-based adhesive.
We maintain stock in both the U.S. and Asia for better efficiency with our manufacturing partners and brands.